Battery industry space: consumer demand is still increasing, and the industry head effect is significant
Traditional consumer electronics shipments slow, emerging markets provide major increments
The consumer electronics market is vast, and the overall shipments of lithium batteries are growing rapidly. According to GGII data, the CAGR of global lithium battery shipments from 2016 to 2020 reached 28%, of which global consumer lithium battery shipments in 2020 will be 131GWh, a year-on-year +48%; China’s lithium battery shipments in 2020 will be 143GWh, of which consumer lithium battery shipments will be 143GWh. Shipment volume was 46.8Gwh, a year-on-year increase of 28.2%. According to GGII’s forecast, China’s lithium battery market shipments will reach 611GWh in 2025, with a compound growth rate of more than 25% from 2021 to 2025.
Traditional consumer electronics: shipment growth slowed down. According to a TrendForce survey, global notebook computer shipments in 2021 will increase by 19.4% year-on-year, reaching a record high, due to the impact of the epidemic on the hybrid office. However, this growth trend may not be sustainable. In 2022, global notebook PC shipments are expected to decrease by 5% year-on-year, and tablet PC shipments will also slow down significantly, excluding the impact of the epidemic. In addition, after years of development, the smartphone market in East Asia, Europe, North America and other regions has become relatively mature. According to IDC data, from 2016 to 2021, the growth rate of smartphone shipments will be in the range of -6% to 5%. According to the 2021 global mobile phone market report released by the Pew Research Center in the United States, the penetration rate of smartphones in the United States has reached 82.2%; the United Kingdom, Germany, France, South Korea, Italy and other countries have reached more than 75%, and the penetration rate of mobile phones in China is 66%. , only a few emerging economies are still at a low level. As the penetration rate of smartphones continues to increase, it is expected that the growth of smartphone market sales will stagnate or even decline, and the smartphone industry will enter the era of stock replacement.
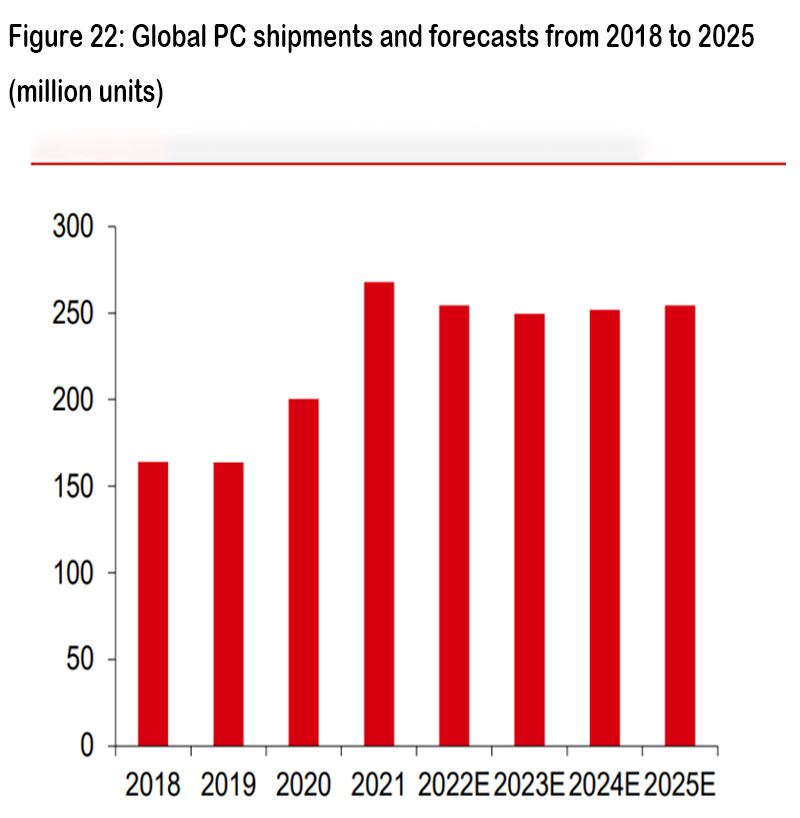
The advantages of consumer soft packs are obvious, and the proportion of shipments has increased rapidly
In terms of consumer batteries: In 2021, the global shipments of notebook soft packs will account for 95.3%. The downstream applications of soft pack batteries mainly include consumption, power and energy storage. Soft pack batteries are favored by consumer lithium batteries due to their high safety, high energy density, high flexibility, and low cost. According to Techno System Research, the proportion of global mobile phone soft pack battery shipments will increase from 54% in 2015 to 89.7% in 2021; the global s notebook computer soft pack battery shipments will increase from 35.8% in 2015 to 95.3% in 2021 .
75.2%/77%/78.2%/78.5%, the trend of thin and light notebooks has become the consensus of mainstream notebook manufacturers; in terms of demand, portability has become one of the primary considerations for consumers to buy notebook computers, and traditional cylindrical 18650 batteries are gradually becoming It is replaced by soft bags with light weight and large capacity, so we predict that the penetration rate of soft bags will increase to 96.2%/97.2%/98.2%/99.2% in 2022-2025, respectively. Limited by the thickness requirements, the tablet battery has been dominated by soft-pack batteries since its launch. It is expected that the share will remain stable in the future, with a penetration rate of 99.7%/99.8%/99.9%/99.9% in 2022-2025, respectively.
With capacity improvement taking into account volume optimization, the share of mobile phone soft cases is expected to increase to 95% in 2025. Driven by Andy-Beer’s Law, software performance improvement promotes hardware upgrades. The average value of a single unit of soft-package single-cell battery used by manufacturers has increased from 33.8 yuan/unit in 2018 to 45.8 yuan/unit in 2021; The penetration rate of 5G mobile phones has increased from 0.71% in August 2019 to 75.9% in 2021. Due to frequent network switching, high screen refresh rate, increased 5G network components, and increased chip power consumption, the battery capacity of mobile phones faces a larger capacity increase Require. Under the trend of thin and light smartphones, soft-pack batteries have become the choice for capacity improvement and volume optimization. It is expected that the penetration rate is expected to reach 93.4% in 2025.
There is still room for improvement in the penetration rate of soft pack batteries in emerging consumer electronics. In recent years, soft-pack batteries have been gradually applied to emerging consumer electronics fields such as wearable devices, electronic cigarettes, drones, and wireless Bluetooth speakers, but the penetration rate still has a lot of room for improvement compared to the traditional consumer battery field. For emerging consumer electronics such as wearable devices, the advantages of soft pack batteries such as lightness and large capacity still exist. Therefore, it is expected that soft pack batteries will also become mainstream batteries for emerging consumer electronics in the future.
The global consumer soft bag space is expected to grow, and the market size is expected to reach 480.2 billion yuan in 2025. According to our estimates, the global demand for consumer soft packs in 2021-2025 will be 73.2/81.2/91.0/98.2/105.4GWh, and the CAGR will reach 7.6% in 2021-2025; the market size will be 2,979/3,344/3,606/3,962/440.7 billion respectively yuan, with a CAGR of 8.1%. Among them, it is expected that the demand for soft pack batteries for notebooks, tablets, mobile phones, and other consumer electronics (wearable devices, AR/VR, drones, Bluetooth headsets, etc.) will reach 15.4/5.5/21.9/62.6 GWh, respectively, in 2025. The space will reach 1128.4/294.6/509.8/247.5 billion yuan respectively, and the main increase in the market will come from emerging consumer electronic products.
In terms of power batteries: in 2021, the installed capacity of domestic power soft pack batteries is 10.3GWh, and the penetration rate is only 7%. From the perspective of the installed capacity, the penetration rate of domestic soft pack batteries in 2021 is only 7%, which is far behind the 42% penetration rate of foreign soft pack batteries. , Ford, Daimler, etc. have a high degree of recognition of soft-pack batteries, benefiting from large subsidies and the launch of new models. In 2020, 15 of the best-selling TOP20 new energy passenger cars in Europe are equipped with soft-pack batteries; on the other hand, Ningde is currently equipped with soft-pack batteries. The three leading companies, Times, BYD, and China Innovation Airlines, account for more than 70% of the installed capacity. They are mainly square batteries, which squeeze the market share of domestic soft pack batteries.
Entering the overseas soft pack battery supply system, the penetration rate is expected to continue to increase. The soft-pack battery has a complex process, high production technology requirements, and an imperfect domestic supply chain, resulting in high production costs. The penetration rate of soft-pack batteries in the domestic market is still at a low level. At present, Funeng Technology has established close cooperation with GAC, Brilliance, Geely and other OEMs in China to consolidate its share. At the same time, it has signed a 170GWh supply contract with Daimler in Europe from 2021 to 2027, and the cooperation with Volkswagen is progressing smoothly; Yiwei Lithium Energy It has entered the soft package supply system such as Hyundai Kia. In the future, with the overseas volume of domestic top power soft pack companies, the penetration rate of soft pack batteries is expected to continue to increase.
All-solid-state batteries have high energy density and the strongest safety, and are expected to open up the growth space for soft packs. All-solid-state batteries use solid electrolytes such as polymers, oxides or sulfides to replace separators and electrolytes to fundamentally solve battery safety problems; the energy density of battery cells is expected to increase to 400-500Wh/kg. Since there is no need to use liquid, the shell and assembly process of solid-state batteries are simplified, and the soft-pack packaging technology suitable for solid-state battery packaging is expected to open up new growth space for the development of soft-pack batteries. European and American companies prefer oxide and polymer systems, while Japanese and Korean companies are more committed to solving sulfide systems. At present, all-solid-state batteries are still in the research and development stage, and new car manufacturers are more accepted. Traditional car companies participate in three different routes: acquisition, cooperation and self-research.